It’s no secret how beneficial the use of a pressure transducer can be. Being able to convert the pressure of the physical world into a voltage signal we can analyze with our scope gives us the ability to quantify things that we wouldn’t be able to otherwise.
In case you aren’t familiar with using a pressure transducer, variables like crankshaft speed and throttle position can radically affect the measurements our pressure transducers give us. One technique that helps eliminate many variables is using 2 sensors at the same time. With one sensor installed into the suspect cylinder and the other installed into that cylinder’s companion, we now have two traces. One from the cylinder we think may have an issue and one that is hopefully a known good.
Since the measurements are taken simultaneously the speed of the engine, throttle opening, temperatures and most other variables are already accounted for and mitigated.
In the following example we’re going to look at a 2011 Jeep Grand Cherokee with a 5.7L V8. This engine has the Multiple Displacement System that deactivates cylinders 1,4,6,7.
The driver’s complaint is that the engine runs rough and the check engine light is on and flashing. A P0302 cylinder 2 misfire diagnostic trouble code was retrieved from the ECM. The client has replaced the ignition coil and 2 spark plugs for cylinder 2.
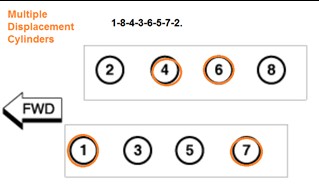
After verifying the rough running and the DTC for ourselves, a tapping clacking type noise was also noted. At this point a relative compression test was performed. While the capture is not an ideal smooth pattern it is stable enough to conclude that we’re not looking for a massive compression leak.
Ignition coil and fuel injector drives were also checked and considered valid.
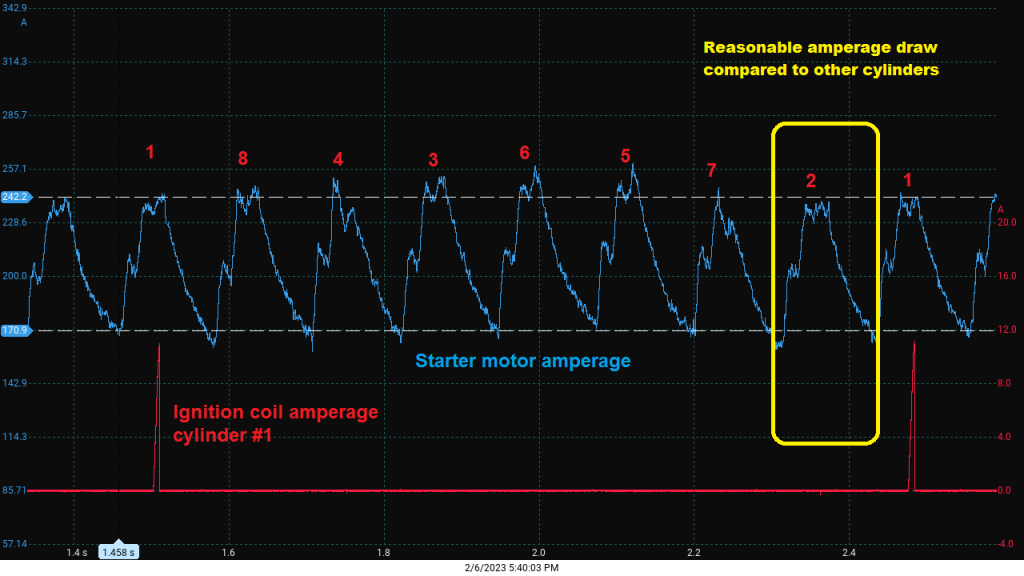
At this point it was time to go in cylinder. The ignition coils and fuel injectors were disconnected for cylinders 2 and 3. This engine’s firing order is 1-8-4-3-6-5-7-2. This makes cylinders 2 and 3 companion cylinders.
With the coils removed and just 1 of the 2 spark plugs per cylinder removed a pair of WPS 500X pressure transducers were installed.A cranking compression test comparing the 2 cylinders starts to show the cause of our client’s complaint. The “nose” toward the end of where the exhaust stroke occurs tells us there was a pressure rise within the cylinder at the time when 1 or both of the valves should have been open.
Remember, this is capture made at cranking speed so we won’t normally see much activity between compression towers.
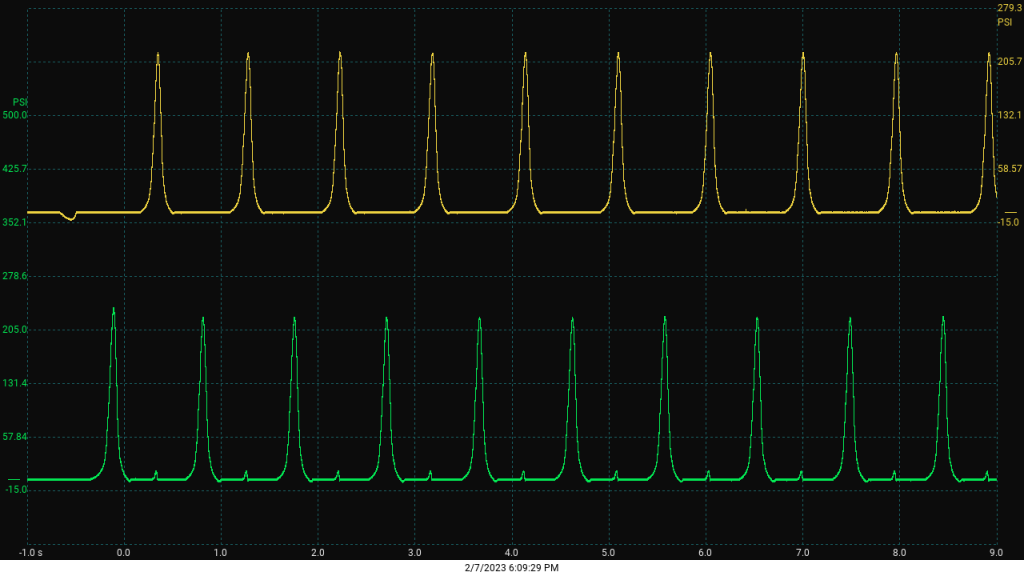
Next the engine was started and while it was running the throttle opened to rev the engine a couple times. Before revving the engine the suspect cylinder had a compression peak of 95PSI while the companion had 102PSI.
The real difference can be seen in the “nose” at the end of the exhaust plateau. That rise in pressure peaked at almost 50 PSI, at idle. When the engine was revved up the pressure in cylinder 2 on the exhaust stroke was over 130PSI!
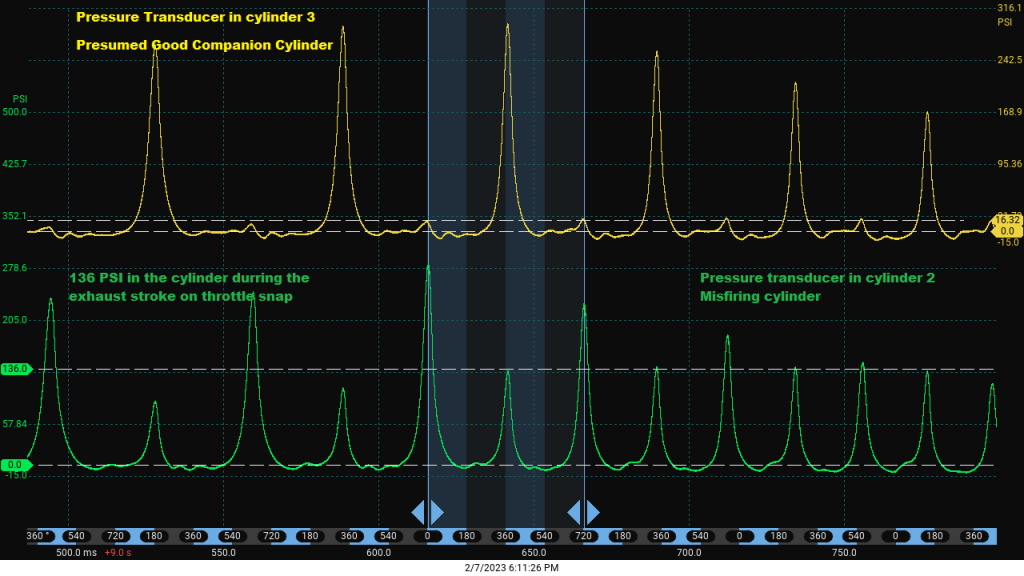
To confirm the diagnosis that the cam shaft has the exhaust lobe worn off for cylinder 2 the valve cover was removed and the engine rolled over by hand. It was observed that the intake valve was lifted open approximately the ½” that it should while the exhaust valve was lifted less than 1/8”.
While this diagnosis didn’t require the use of 2 transducers, it did make explaining the issue to the client easier.